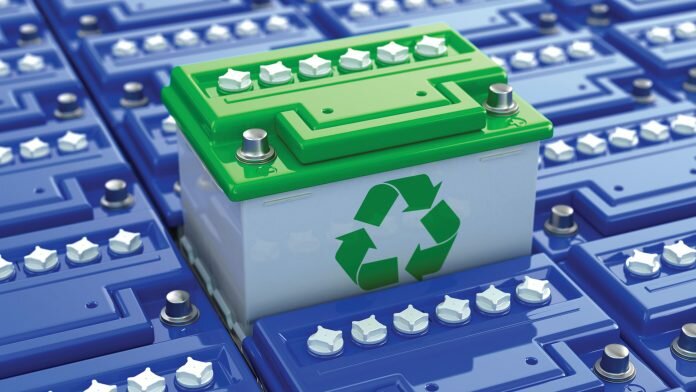
Waste management and recycling team Aurelius Environmental is piloting a green, low-cost and highly efficient process for recycling of lead-acid batteries
Founded in 2014, Aurelius Environmental Limited (AEL) is a visionary and innovative process and service company. We operate in the area of environmental management, recycling and treatment of waste – particularly in relation to lead-acid battery recycling and the associated waste streams. Our mission as a company is to revolutionise the waste management and recycling industry.
We aim to add real economic and societal value to the markets in which we operate, while investing in the local and wider communities to achieve sustainable development and a strong social and economic ethos in our delivery to market.
Our vision is to create a fully sustainable business, where waste streams enter our processes and nothing but products leave, and where multiple recycling infrastructures complement each other, with one stream’s waste being another stream’s in-feed. The first stepping stone towards this vision is a technology for the recycling of lead-acid battery paste.
In partnership with the University of Cambridge, UK, we are piloting this hydrometallurgical process as a potential alternative to waste battery paste de-sulphurisation and/or smelting. It is a zero-emission, low-carbon footprint, energy-yielding process providing a step-change in the greater industry for the recycling of lead.
Where we are
At Aurelius, we have extensive knowledge of the waste and recycling industry. We have a proven track record as an established waste management business that accepts, processes and recycles over 10,000 tonnes of used lead-acid batteries per annum. Our forecast for 2018 is processing up to 15,000 tonnes of lead-acid battery waste.
The principal technology, trademarked as Fenix-Pb, was originally invented at the University of Cambridge by Dr Vasant Kumar. In 2016, it was licensed exclusively to Aurelius, and since then we have been piloting and further developing the technology in collaboration with Dr Kumar. Our piloting efforts are supported by three major grants – two Innovate UK awards and a grant from the prestigious Horizon 2020 SME instrument – which have raised a total of over £2,000,000 in funding.
The commercial success of our patented process lies in its low cost and scalability, as well as our ground-breaking ability to produce LAB-ready products that exceed the performance of current products on the market. Our green credentials include:
- Reducing the carbon footprint of paste-recycling by over 80%;
- Eliminating noxious gases (such as sulphur dioxide and nitrogen dioxide) without having to separately de-sulphurise the paste and/or deploy abatement technologies; and
- Releasing (rather than consuming) energy of up to 400 mWh per 1000 tonnes of batteries processed (with this energy being released during the calcination stages).
Crucially, our process enables the production of battery-ready lead oxide directly from waste battery paste – in other words, without first having to produce an intermediate lead ingot. This has the potential to significantly reduce the cost of the overall battery manufacturing process. In addition, it enables the battery industry to use its own waste directly for the manufacturing of lead oxide – going from waste lead sulphate to battery-ready lead oxide directly.
In parallel to the green credentials provided by Fenix-Pb, laboratory batteries manufactured from our proprietary lead oxide are up to 30% more energy dense compared to primary lead-acid batteries. This is because our hydrometallurgical process affords a nano-structured lead oxide; an oxide whose particle size distribution is not only smaller, but also more consistent. We can control the proportion of free lead particles in the final product, as well as the ratio between the alpha and beta forms of the oxide. This enables unprecedented control of the composition and consistency of the lead oxide.
Lead-acid battery industry overview
The recycling of lead is a colossal business. In 2013, global secondary lead production rose to 6.1 million tonnes (source: ILA). All the lead produced in the US is secondary lead, while in Europe it comprises 70% of the market.
Lead-acid batteries are the primary application for all this lead. In Europe and the US, almost 100% of used lead-acid batteries are recycled to create so-called ‘secondary lead’. This impressive statistic proves that lead is one of the most successfully recycled materials in the world.
Lead can be recycled indefinitely with no reduction in quality, and a lead-acid battery is known as the world’s most recycled consumer product (source: ECOBAT, BCI). The global lead-acid battery market is forecast to reach USD 84 billion (~€67bn) by 2025. This is driven largely by expansion of the automotive industry in developing countries, including Brazil (source: Research and Markets).
The recycling of lead batteries via current methods produces ‘smelter smoke’ – a toxic mixture of sulphur dioxide, nitrogen dioxide and often lead particles. It is ironic that lead recycling is motivated by a desire to achieve sustainability, and yet the recycling processes in use today are damaging the environment. The recycling of lead has come a long way, but it is not yet sustainable. Our hydrometallurgical process, Fenix-Pb, is a step closer to sustainability, economic and low environmental footprint recycling of the waste battery paste.
Fenix-Pb – towards sustainable green recycling
Fenix-Pb uses refined mechanical separation and a patented hydrometallurgical process to afford a proprietary lead-oxide battery paste. The key benefits offered by our process and product include:
- No harmful emissions – unlike smelting, our lead recycling chemistry does not release any gases harmful to the environment. This is a major step towards sustainability;
- Energy is a product of the reaction – the chemistry is highly exothermic, producing energy that can be fed back into the system or stored. Whereas smelting consumes anything from 2-10KwH energy per kilogramme of battery recycled, our process consumes a mere 50Wh (roughly the same amount of energy that the battery produces); and
- Instead of only producing lead ingot, we produce ‘battery-ready’ lead oxide, which can be used to manufacture new batteries. This avoids the downstream re-processing of lead to lead oxide, leading to cost savings and a higher quality lead oxide.
Due to the superior quality of our lead oxide, batteries made from our product can be at least 30% more efficient than regular lead-acid batteries. These key benefits deliver four important outcomes:
- We can produce a more energy-dense battery;
- We can control the ratio of alpha to beta lead oxide, as well as the proportion of free lead metallic lead particles, providing fine-tuned products for unique applications;
- Our capital expenditure is low – we are economically viable even with a much smaller processing capacity than a smelter. This allows us to be profitable even in remote areas, and in developing or emerging countries where facilities can be positioned closer to the source of the waste batteries; and
- We improve efficiency, lower transport costs and allow for economic and safe recycling anywhere in the world. For every 10,000 tonnes of batteries processed we expect to generate between $2.5m and $5m (~€2.2m and €4.4m) more gross profit than smelting, depending on the cost of the reagent, citric acid.
Technology
Our technology is based on an ambient temperature hydrometallurgical process, replacing the comparatively hot, high-energy processes used in pyrometallurgy. The individual steps involved, carried out once the paste has been neutralised, are as follows:
1. Leaching crystallisation
Non-toxic carboxylic acids are added to the neutralised paste. Unlike other hydrometallurgical processes, our lead is not solubilised in the leachate and we do not use electro-winning. This is a significant advantage, because electro-extractions are expensive in terms of the energy cost and use of electricity. In our process, what follows is the crystallisation/precipitation of an organic precursor containing lead. The carboxylic acid used in this process is citric acid.
2. Combustion/Calcination
The precursor is heated to 300-400°C to remove organics and release lead. These organics serve as fuel in the combustion process, thereby assisting the calcination process and lowering the energy cost. The decomposition liberates a mixture of metallic lead and lead oxide. The degree of oxidation depends upon the operating conditions.
By varying the combustion/calcination conditions through our process controls, it is possible to control the ratio of alpha and beta forms of lead oxide produced. Most importantly, lead oxide is produced in nano-crystalline form. According to laboratory studies, this lead oxide is up to 30% more efficient than that produced by traditional methods, even from ultra-pure lead.
In other words, our process is not only low-cost and environmentally friendly; we eliminate the need for downstream re-processing of lead to lead oxide. In addition, our lead oxide is (as per laboratory testing) up to 30% more efficient than anything offered in the market today.
3. Lead-sulphate recovery
Any residual lead sulphate (PbSO4) can be recovered in the calcined lead product in the form of a binder. Noxious gases, such as sulphur dioxide, are therefore eliminated without the need to deploy abatement technology. Other products, including lead sub-oxide and metal lead, can be obtained using the same procedure. At little extra cost, the chemical composition of these products can be controlled.
Importantly, this process works with both lead and lead alloys, although the latter require additional refining steps. The lead oxide can be used to manufacture new batteries without further processing – and, as has been already explained, with an increase in energy density by up to 30% (as per laboratory testing).
Target market
Lead is a globally traded commodity with a worldwide market value in excess of $20bn (~€16bn). Yet, most lead mines are becoming exhausted. Coupled with rising global demand, recycled lead makes up roughly 57% of all lead produced worldwide. There are no economic alternatives to lead batteries for starting, lighting and ignition in automotive applications, and lead-acid batteries continue to offer the cheapest and most reliable source of energy for many old, new and emerging technologies.
Extremely high growth rates in lead consumption are forecast in emerging markets for decades to come. Yet capital costs for installing pyrometallurgical process plants with full environmental control for recycling lead are high. This leads to so-called ‘informal sector’ recycling, where the escape of lead to the environment causes pollution and poisoning of local communities.
A new, environmentally friendly, low capital-cost process will have major global impact. Our technology can deliver this and so much more, as it is more profitable than traditional smelting plants and produces a superior, more efficient lead-acid battery. At Aurelius Environmental, we seek to set up our own recycling facilities, but will also evaluate joint ventures and licensing arrangements. With our UK pilot plant due to open in 2018, we are paving the way for companies around the world to join us on our mission to deliver next-generation recycling – with corporate responsibility, sustainability and a brighter future for all.