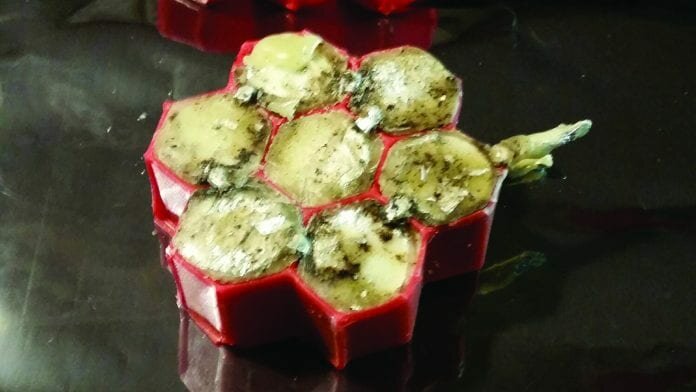
JAKERTECH uses battery injection moulding, an established manufacturing technology, to develop products faster and cheaper than any other fabrication methods.
Marc and Kim Jaker both have a long history in corporate management, materials, design and manufacture. They have used their knowledge to develop this new manufacturing platform, using battery injection moulding – the new process allows JAKERTECH to mould with greater detail, meaning they can also mould the wiring. The design is fundamentally an established manufacturing technology that delivers a quicker and more cost effective fabricating method than most.
The science: how does battery injection moulding work?
JAKERTECH has developed a new manufacturing platform for electrochemical cells, using injection moulding for batteries, ultra-capacitors and fuel cell plates – probably best suited for cell packs. The amount of detail that can be moulded in the parts, means that JAKERTECH can mould the wiring, threads, retainer clips, etc., thus incorporating a multitude of secondary assembly parts in the geometry. Due to the nature of bolts and screws, they can often become loose and welds often breaks, however, solid single piece structures are always better in the long-run, especially when vibration is involved.
JAKERTECH holds intellectual property rights for this new specific battery injection moulding process; the products can be moulded as individual cells in large multi cavity, multi shot moulds, or as battery/capacitor packs, of around 4-1000 cells at once for cordless tools, electric vehicles, stationary storage, or as large format cell plates. Additionally, as the wiring/bus bar can be moulded in series or parallel as an integral part with the electrodes, thereby reducing the labour costs. It is conceptually similar to the etched circuit board in electronics, the difference being, here it is using injection moulding rather than being photo or acid etched – the big assembly labour costs disappear and the rate of production increases.
Due to its ability to incorporate a myriad of geometric features, there are fewer total components. Cells share walls next to each other, the retainer tray is also the outer wall of the cells and the separators are no longer there. This method can hold much tighter dimensional tolerance, depending on the resin type, resistance to corrosion or other chemical reactions is zero. In one design, the cells are all hexagonal (a reflection of one of natures’ most efficient shapes) and the electrolytes are solid, not liquid or gel like many conventional batteries.
Because they are composed of polymer alloys, cells can be injected under several thousand pound-force per square inch (PSI) or pascals, applying pressure and using heat. This fuses and surface blends the entire polymer alloy matrix, one layer to the next, making it one solid mass. Separation is inherently less probable (no air bubbles, gaps, voids) even under hard field use. Additionally, due to this novel battery injection moulding approach, new large format cells with conformal geometric shapes become possible. As all ‘plastic’ parts, they can be made to look like anything you can imagine; bonnet, roof, door, seat backs, wheel wells, dash board, etc. Using JAKERTECH’s method, they don’t just have to be the round cylinders or flat packs that are so common today.
It is also adaptable to many different chemistries, just about anything that can take the heat, beyond lithium. Whatever the chemistry was, now it will perform better. These solids are much less likely to heat up and explode like Lithium as there are no solvents or flammables in the mix. By using self-extinguishing/flame retardant additives they can actually help put out any fire that may arise from surrounding sources, so safety is dramatically improved. There are several ways beyond removing the metal casings and metal trays that weight can be reduced, such as more efficient geometries, using common walls between cells, by injecting nitrogen into the resin, making the binder resin even lighter and potentially much stronger. This means that battery injection moulding may even be suitable for manufacturing structural components in aircraft and enhancing the all-weather mobility of automobiles.
This is a game changer in terms of cost reductions (removing capital and labour – a key factor which is imperative for the west to compete), physically more robust electrical storage units, higher capacities, lighter weight (no individual metal cans/redundant wall sections and heavy metal trays and boxes for the packs), new product designs, new applications and geometric options. Battery injection moulding is a way to make lots of things quickly; plastic is everywhere – for better and for worse. To recycle, they can debind/separate the polymer, chemically or by using heat from the ‘active’ fillers and start all over again. Current Lithium recipe batteries are extremely difficult to recycle and this is an area where JAKERTECH excels. Charge times have also been known to be very fast, but there are a lot of dependent factors. Complex electrical and thermal management systems appear to be obsolete, the whole design is just simpler.
As for ultra-capacitors or super capacitors – which can also be manufactured using battery injection moulding – they are much simpler to manufacture; ceramic filled resins sandwiched between two metal filled resin plates. The main difference is the absence of electrolyte, they can store large amounts of electrical current, they charge and discharge extremely fast (seconds vs. hours) and they typically last million(s) of charge/discharge cycles. These are also assembled and built into cell packs. JAKERTECH anticipates that the future will be in hybrid battery/capacitor packs, which further obsoletes Lithium. Ultra-capacitors are currently widely used across sectors, they take up the void in power loss in substations and are in modern start/stop internal combustion engine cars.
The technology
The chemistry is the same as that of current batteries; however the particle sizes, geometry and concentrations are all different. Simple Alkaline, NiCad, MiMH batteries have several recipes which accommodate a specific battery size or design. However, JAKERTECH have found that there are carbon nanotubes which can augment basic solid state electrical conduction. The multi-shot battery injection moulding process can be done using horizontal or vertical presses. The first shot injects material into the cavities, the mould plates with the cavity detail are then rotated around to the next material station/barrel. They are then spun or turned on a cube, ready for the next shot of material, thus building up the layers and therein building the battery in a mould. These layers are shot under high injection pressure (in the rough range of high powered gun) and simultaneously the melted resin part of the alloy melts into the previous shot, forming a hermetic bond.
The whole process is alike to that of metal welding technology, with many similarities to metal injection moulding (MIM), ceramic injections moulding (CIM) and powder injection moulding (PIM), the main differences being that JAKERTECH does not debind or sinter. MIM and CIM are beneficial in that they are the modern way to make highly complex and small parts for micro surgical tools, medical devices and guns; favourably competing with Swiss multi axis machining technology. However, with the JAKERTECH’s battery injection moulding approach, it all remains in the green state; the binder resins are not HDPE+ beeswax, but strong, tough engineering grade resins such as Urethanes, Nylons – 6/6, 6/11, 6/12, Polyesters and LCP.
These highly filled resins then tend to flow more akin to a slurry than a plastic resin of high melt flow index. Battery injection moulding requires more knowledge than conventional plastic moulding, however, this is a relatively small learning curve for the technician on the floor. Runner systems and gates in the mould must be adjusted accordingly. Additionally, should the design require a stamped component, it is possible to insert these robotically in the cycle. This is a simple addition or removal option in the moulding press or work cell. In efficient and modern manufacturing, it is imperative to execute as many operations/features in an assembly as possible. This is rule 101 of cost reductions and global competitiveness.
The challenges
After numerous trial and error attempts using nano- and microparticles, JAKERTECH came into their element once they realised this was the wrong direction. JAKERTECH uses large particles of 250 micron or larger in its battery injection moulding and have since seen no failures. The particles need to be able to “touch” and depending on the geometric shape of the active components, the cross sections form a plywood or birds’ nest type structure imbedded in resin. It is important that the geometries should be three dimensional and not flat (2D); they must be bent, curved and twisted to enable them to touch, conduct and store at all times.
The binder resins cover virtually all thermoplastics with the deciding criteria being cost and performance objectives; from flexible elastomers for flexible battery applications, to rigid, high strength, super tough polymer resins for rugged applications.
With JAKERTECH’s battery injection moulding technology, dendrite formation is extremely unlikely, in their design, heat seals and melts the thermoplastic which in turn seals and blocks the formation. The cells are extremely difficult to kill, unlike in current batteries, thus meaning they are likely to last a lot longer with whatever chemistry you choose. You can cut them up into pieces, only making lots of little batteries (needing to be rewired) or shoot a bullet through them, which just reduces the capacity by what was blown away. A very different thing from lead acid batteries.
The future
Of the tens of thousands of plastics moulding plants around the world, around 10% of these facilities could make these with only minor modifications to their equipment; dependent on press sizes, shot sizes and the size of the battery or battery module. Battery injection moulding plants are inherently designed and built for constant operation due to the time it takes to boot up a system, get the presses to soak and stabilize whilst reaching the sufficient temperature for resin processing. Old chemistries will be improved dramatically, so there is no longer a strong need to worry about who is hoarding Lithium, Cobalt or other raw material deposits in the world. It could further democratise the electrification of things we enjoy and have come to depend on.
As the physics and chemistry of solid state batteries means they will not freeze or boil, it allows for a greater range in operation temperatures. Adding light, self-sufficiency and self-reliance to remote communities which would benefit from electricity could open up the habitability of uninhabited, desolate areas (in many countries and regions like the western USA, Eastern Russia, Africa, Arctic and sub-Arctic). Electricity allows people to pump water, communicate, heat, cook, cool and be mobile with electric bicycles, scooters, cars, trucks, trains, boats and light aircraft by generating electricity with solar, wind, hydro and wave actions as we move towards a greener world.
Summary
The key point to the battery injection moulding technique developed by JAKERTECH is reducing manufacturing costs. Depending on the chemistry (the cost of specific raw materials used), geometric configuration, and the number of cells. Those reductions can range from 20 to 70 per cent compared to today’s methods. This is how JAKERTECH could make it cheap enough for everyone to participate in this potential continuation and evolution of civilisation.
JAKERTECH is bringing several technical disciplines together, projecting a technology platform which has low costs, produces products which are lightweight, have higher capacities and a greater temperature range: battery injection moulding is simply a logical evolution of technology. Even 96-year-old professor and father of the lithium battery, Dr Goodenough, has described battery injection moulding technology as ‘making sense’.
JAKERTECH are looking for licensees and/or partners to develop their technology platform with rapid commercialisation objectives. Ideally this would be a multidisciplinary team, with wise public sector visionaries and their funding assistance.
Marc Jaker
CTO Founder
JAKERTECH
+1 612 801 8099