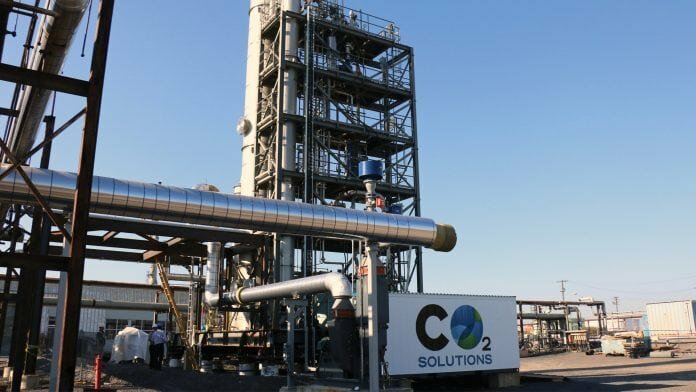
Samuel Lethier explains how Total is contributing to the industrial deployment of carbon capture, utilisation and through innovation clusters with industry actors, start-ups, academics and government bodies.
According to the Intergovernmental Panel on Climate Change (IPCC), which is the leading international scientific body for the assessment of climate change, “human influence on climate change is clear, and recent anthropogenic emissions of greenhouse gases are the highest in history. Warming of the climate system is unequivocal, and since the 1950s, many of the observed changes are unprecedented over decades to millennia. The atmosphere and ocean have warmed, the amounts of snow and ice have diminished, and the sea level has risen”.
Carbon capture and storage (CCS) is recognised by the IPCC as essential in the mix of carbon mitigation technologies (such as energy efficiency and renewable energy) required to limit climate change and its effects. In the same fashion, the International Energy Agency (IEA) believes that CCS is vital for reducing emissions across the energy system and for keeping the average temperature increase to below 2°C.
Combatting climate change is one of the biggest challenges facing everybody in this century. CCS and more broadly CCUS (carbon capture, utilisation and storage) are part of the solution.
Special focus on industries with “process CO2”
Anthropogenic or man-made CO2 is a by-product of human activities. Unfortunately, most often in the industrial and power generation sectors, it is not generated at high enough purity to be directly transported and ultimately stored. It has to be captured, which consists of separating the CO2 from the other constituents of the main stream, most commonly referred to as flue gas. A few examples of CO2 concentrations in various flue gas:
- gas power plant: 3 to 5%;
- coal power plant 10 to 15%;
- iron and steel industry: 20 to 27%;
- cement plant: 14 to 33%; and
- Steam Methane Reformer (SMR) process 30 to 45%.
The main targeted point sources for CO2 capture are the power generation and industrial sectors, with special emphasis on industries for which CCUS is the most promising solution that can lead to deep cuts in CO2 emissions, while minimising the performance impact on the industrial process or the final product quality: the iron and steel sector, the cement industry, refineries, pulp mills and waste incineration.
Some industries exhibit the particularity of having a dual CO2 source: the “combustion” and “process” CO2. The combustion CO2 results from the combustion of carbonaceous fuels such as coal, oil, gas, or biomass, whereas the process CO2 is the result of a chemical reaction required to manufacture the desired end product. A few processes among the largest point source CO2 emitters that inherently produce CO2 are:
- The reduction of iron ore into iron (Fe2O3 + CO → 2Fe + 3CO2);
- The calcination of limestone into lime (CaCO3 → CaO + CO2) to produce clinker and ultimately cement; and
- The water-gas shift reaction in a SMR to produce hydrogen (CO + H2O → CO2 + H2).
As stated by the European Cement Association, “even with the most efficient processes, a part of the CO2 emissions linked to cement production cannot be avoided.” Typically, the CO2 directly released from the processing of limestone represents 60% of the total CO2 emissions, and carbon capture has great potential to enable significant reductions.
Industrial units having a significant fraction of process CO2 and at the same time, relatively high CO2 concentrations are the most relevant targets for short/medium-term deployment of CCUS. They typically are the iron and steel as well as the cement industries along with the hydrogen production units in refineries.
Equinor, Shell and Total are major actors in the full-scale CCS project in Norway which aims at accelerating the commercial deployment of CCS. Not surprisingly, this project is targeting a cement plant and a waste to energy facility (incinerator) as the CO2 sources. It marks the start of a future industrial CCS cluster in Norway, welcoming other industries to join forces in the future.
Total who has the ambition to become a leader in CCUS is stepping up its efforts in developing integrated solutions applicable to the above-mentioned industries.
Carbon capture – from short-term deployment to disruptive technologies
CO2 capture technologies can be classified in three main categories:
- Post-combustion capture (or PCC) with consists of separating CO2 in flue gas;
- Oxy-combustion which separates O2 from the air in a combustion process; and
- Pre-combustion converting a fossil feedstock to CO2 and H2 prior to combustion.
These categories share similar separation strategies including solvents for absorption, solid sorbents for adsorption, membranes and cryogenic processes. Even though various technologies have commercial applications today (amine-based solvents being the most widespread), mainly in the hydrogen, ammonia and food industries, the scale at which they are deployed is at least an order of magnitude less than what is required to decarbonise the average size steel mill or power plant. Also, in these commercial applications, the cost of separation is offset by the market value of the end product. Large-scale deployment of anthropogenic CCUS needs an economic incentive, and surely, the lesser the cost of CCUS the sooner the deployment.
A CCUS value chain comprises capture, conditioning and transport and finally injection and storage or utilisation of the CO2. The cost of carbon capture usually represents significantly more than half of the whole chain cost. Specific efforts have to be made to drive costs down (both CAPEX and OPEX), while improving robustness to flue gas contaminants, minimising the environmental impact, reducing footprint and complexity of operations.
At Total, our R&D CO2 capture efforts can be divided into two categories: technologies for the short/medium-term deployment and the longer term.
For the short/medium-term, we are contributing to collaborative developments with start-ups and industrial partners, focusing on promising technologies at the pilot plant maturity level. The main challenges are to develop solutions compatible with real industrial flue gas and to integrate the capture unit within the existing plant to optimise the heat recovery and contain the overall parasitic load. Our participation in Technology Centre Mongstad (TCM) in Norway, one of the world’s largest carbon capture testers and development infrastructure is one example. Also, Total recently kicked-off the CHEERS project (Chinese-European Emission-Reducing Solutions) alongside Chinese and European partners to demonstrate a 3MWth Chemical Looping Combustion (CLC) process. The CLC process has a potential for a major energy penalty reduction. Other pilot plant projects are in preparation with industrial partners.
For the longer term, we are aiming to develop disruptive technologies with the ambition to cut down costs by half compared to today’s commercial technologies. Such a steep change requires innovative research approaches to identify advanced materials and matching processes leading to breakthrough solutions. Successful research will entail state of the art computation tools, such as; artificial intelligence, molecular modelling, quantitative structure property relationships, high throughput material characterisation and testing. Inspired by the pharmaceutical industry research, innovation will be driven by coupling of science and hi-tech enabling tools.
In the end, it is the development of a CO2 market that will drive the CCUS deployment
The cost impact of CCUS on a specific industry decreases substantially at each transformation stage. A study performed by Johan Rootzén & Filip Johnsson concludes that the cost impact of CCUS on a cement plant will only have a 1% increase in the overall cost of a residential building, even though the cement price is doubled. In the same fashion, at a carbon price of 100€/t CO2, the retail price of a mid-size European passenger car would only have to be increased by about 100 € (0.5%).
Climate change is one of the biggest challenges facing every country and every person in this century. It is through innovation clusters composed of industry partners, academics, start-ups, research institutes and government bodies that we will succeed in developing more affordable and user-friendly technologies, whilst at the same time, establish the conditions for a CO2 market. Such a deployment will also require a favourable economic and regulatory environment that will enable engagements guaranteeing the long-term availability of CO2 transport and storage, a mandatory condition for industries to invest in CO2 capture infrastructures.