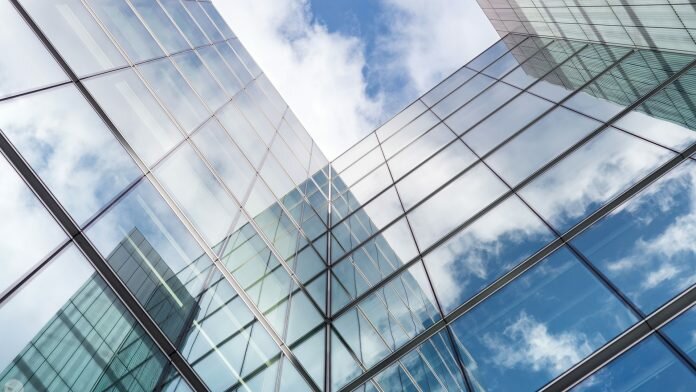
Chris McDonald, CEO of the Materials Processing Institute, UK, discusses the future of materials processing, the action required at a policy level and the implications in advancing towards Industry 4.0.
Industry 4.0, as an expression of the technologies that are enabling the 4th Industrial Revolution, is transforming the global materials sector. From autonomous mining through advanced steel processing to additive layer manufacturing, the whole nature of manufacturing value chains are being rewritten.
Materials as an industry is the foundation of any modern economy and this will remain, but even more so, with both materials and design being the only sure means of generating value in the future economy as traditional areas, such as:
- Machining;
- Fabrication; and
- Assembly risk falling into obsolescence.
From a policy perspective this creates a huge challenge, as the societal upheaval associated with this, as with all previous industrial revolutions, begins to subsume many professional roles. An appropriate policy response is required which both captures the opportunities from new industries arising from these technologies and enables individuals to transition to this new economy.
What is Industry 4.0?
Industry 4.0 is a term coined by technologists and industrialists, to describe a suite of technologies based around automation and digitisation that collectively have the potential to:
- Standardise processes;
- Increase productivity; and crucially
- Reduce the labour required to deliver goods and services.
The conversation to date has largely, and unhelpfully, been driven by a discussion of the technologies without regard to the bigger picture of social consequences, leading to radical changes in the way people live, work and interact socially. There is a policy imperative to recognise that this, the 4th Industrial Revolution, is happening now and it is the fastest, most radical period of change in human history.
Previous industrial revolutions led to new opportunities, new industries and rapid improvement in the outlook and wellbeing of humankind. There is no reason to assume that the 4th Industrial Revolution will be any different. However, in the sweep of history, it is easy to overlook that the higher benefits and advances experienced one, or two, generations later, arise from the sacrifice of those actually caught up in the times of change.
By way of example, consider the analysis conducted in 2013 by The United States Bureau of Labour Statistics which forecast that approximately half of the jobs today would be delivered by machines within 20 years.1 A suite of technologies aimed at improving the perception and decision-making capability of machines, collectively known as artificial intelligence (AI), are poised to subsume a range of skilled and professional roles that have previously been immune from automation, including teaching assistants, accountants and auditors.
This trend has been observed in the materials processing industries, where continuous relentless innovation has produced advances in productivity over many decades. The combination of these technologies – with AI – in an Industry 4.0 approach, presents the opportunity to break through this trend and create a step change in productivity, not seen since the introduction of continuous casting to the steel industry in the mid-1970s.
How can Industry 4.0 technologies be applied to the materials processing industry?
Since the dawn of the 1st industrial revolution, the materials industries have provided the foundation to the modern economy. Global industrial sectors, such as automotive, construction, transport, electronics and aerospace, are built on the advances in materials such as:
- Steel;
- Ceramics;
- Glass; and
- Composites.
These industries have long been at the forefront of Industry 4.0 and digital technologies. Steel in particular has been a leader in fields such as big data and AI since the 1990’s, with progress proceeding as rapidly as computational power allowed.
Many of these technologies have been, and continue to be, developed at the Materials Processing Institute in Middlesbrough, UK. The Institute is an independent not-for-profit entity that was formerly the in-house corporate laboratory for British Steel, and latterly Tata Steel, and it is here that many devices for automation and control for the global steel industry have been developed to global commercialisation. At the Institute, a four-stage model has been developed and successfully applied for full application of Industry 4.0 technologies. The four stages are:
- Measurement;
- Monitoring;
- Expert system; and
- Closed loop control.
Stage one: measurement
The path for such development follows a well-trodden route which starts with a manufacturing process such as the Blast Furnace, which, whilst commercially successful, may have some inherent variability, perhaps due to raw materials.
The first phase of development is to invent an instrument, or measurement device, to provide monitoring of a key aspect of the process; this device may start as an offline diagnostics tool before progressing to full online continuous capability. For the materials processing industries, such devices will generally have to survive hot, dusty, hostile environments and so technologies are found in common with other challenging environments, such as nuclear and space.
An example of this is the online X-ray fluorescence (XRF) measurement technology, developed to monitor environmental emissions from steel plants, which evolved from technology applied by NASA for space exploration.
Stage two: monitoring
With measurement resolved, the next stage is to provide some data interpretation. Often referred to as ‘condition monitoring’ at this stage of development, charts, trends and alarm levels will be relayed to an operator, or engineer, who would interpret the data further and decide on potential actions.
Here, the Institute has developed systems that can utilise acoustic emission monitoring to advise engineers on the precise time to order replacement components which might have a six-month lead time. Before the development of such systems, manufacturers were obliged to keep a large inventory of spares, limiting the availability of working capital and risking obsolescence.
Stage three: expert system
The third stage of development is where AI starts to become apparent, as the machine itself starts to assume some of the responsibility for deciding and recommending a course of action. The Materials Processing Institute has developed many such systems for control of ironmaking and steelmaking processing equipment that can combine process and engineering data with learned experience through a ‘case based’ reasoning approach to provide advice. These instances where advice would be required could include:
- Reasons for equipment failure;
- Quality concerns; or
- Predictive maintenance.
Such systems can include hardcoded intelligence from industry experts, as is the case with the ‘Steel Plant Diagnostics’ system developed at the Institute, which gives a post-mortem analysis of each batch of steel produced and contains the wisdom of multiple industry experts to provide operational advice.
Stage four: Closed-loop control
The fourth and final stage of development occurs when the recommendations made at stage three are implemented entirely by a machine in a closed-loop system. At this point all human interaction and intelligence has been removed, with processing entirely reliant on measurement, monitoring, interpretation and control. Such a system requires the integration of sensors, control systems, algorithms and databases, as well as requiring feedback, learning capabilities and foresight. Technologies developed at the Institute for closed-loop control of the steel furnace are examples of this.
Future opportunities for change
The pathway described above shows how digital technologies can be applied to existing processes and systems, but integration of these technologies gives the potential for more far reaching and radical transformations of both product and service delivery. For example, Additive Layer Manufacturing (ALM), also referred to as 3-D printing, is beginning to revolutionise and disrupt both the materials industries and the manufacturing supply chains that they serve.
The potential for ALM is to produce goods, or components, using less material and in a more flexible manner. A simple consideration of the set up and tooling costs of a component factory. The flexibility of a bank of ALM machines, or a dispersed but interconnected group of machines serving multiple clients at different locations, shows how the whole concept of the ‘factory’, a staple of industry since the mill towns of the first industrial revolution, are being challenged.
ALM has many challenges to be successful, not least the unproven performance of components in many demanding applications when produced from single layer sintering, as compared with the highly engineered microstructure of conventional castings. For this reason, it is likely that the most extreme predictions for the disruptive nature of ALM will not be realised, but there is still the potential to render whole sections of the manufacturing value chain, from machining to fabrication, utterly redundant. This will impact not only the factory’s making components, but those which make the machines that make the components, and so on. In the end, the only sure pieces of the value chain to remain are materials and design, and it is here that investment is required to secure an advantage.2
How can the future of materials processing be secured?
The examples of the materials processing industries have shown how Industry 4.0 technologies can be systematically applied to create a step change in productivity and performance. The integration of these technologies will foster a 4th Industrial Revolution that will disrupt and reconfigure existing supply chains, as well as notions of product and service delivery which are already taking place. Value in an economy will continue to reside in both materials and design, but other areas such as machining and fabrication may become redundant. A policy response is required to capitalise on these technologies and support the transition of people and economies to this new era.
References
- ‘The Future of Employment’: Frey and Osbourne, US Bureau of Labour Statistics, 2013
- ‘Goodbye EU; Hello World – A Vision for an Innovation Centred Industrial Growth Strategy for the UK’: C McDonald, Materials Processing Institute, July 2015
Chris McDonald
CEO
The Materials Processing Institute (MPI)
https://www.mpiuk.com