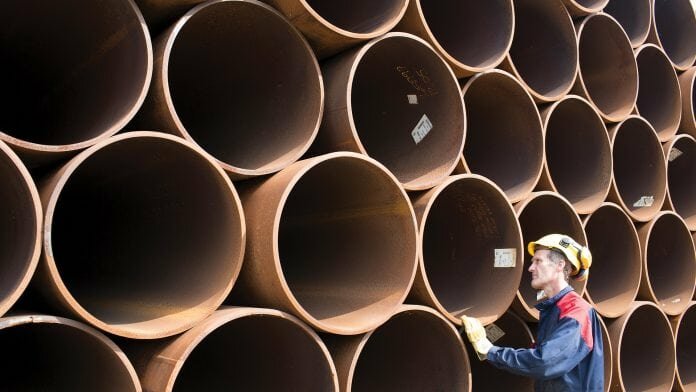
Construction projects utilising surplus steel are achieving huge environmental savings. However, legislation may hamper further growth.
Recent studies have found that using surplus steel for construction projects can achieve carbon savings of up to 96 per cent. However, the unclear wording of building safety standards is creating reticence among some contractors when it comes to taking the step forward in sustainability.
The two key sets of legislation are EN 1090 and the Construction Product Regulations (CPR). EN 1090 requires that all steel used in construction meets the required grade. It does allow for alternative grades of steel, but it is ambiguously worded and not explicit. Furthermore, CPR was never intended to address the requirements of the circular economy, so it looks unfavourably on materials reuse altogether.
If an alternative to newly-milled steel is used, then its properties must be demonstrated via independent material testing. Unfortunately, some organisations interpret the regulations as meaning only new steel or steel certified to 3.1 mill-produced certification can be used. Clearly this inhibits the use of reused or surplus steel.
Roy Fishwick is managing director of Cleveland Steel and Tubes Ltd, a UK-based leading supplier of surplus steel for infrastructure and construction projects. He said: “We have the capabilities to test the integrity of steel to an even greater level of detail than the standard tests at a steel mill; but the regulations prevent us from issuing the 3.1 certificates that some customers are insisting on having.”
A common fault line running through the legislative process is that there are often two bodies of policy makers working in isolation. Roy added: “In the UK, the Department for the Environment, Food and Rural Affairs is responsible for the circular economy and improving sustainability of business. However, the Ministry for Housing, Communities and Local Government is responsible for regulating construction projects and construction materials. This duality is commonplace across the EU; so along with legislative changes to enable wider use of surplus steel, we would love to see more joined-up working from both sides of the policy divide.”
Emissions study
Celebrating its 45th anniversary in 2018, Cleveland Steel has established itself as a leading supplier and stockist of surplus pipes.
Its inventory is comprised of tubes recovered predominantly from steel mills and the oil and gas industry. For the most part, the pipes are surplus stock that is produced to a high standard but never actually used. Cleveland Steel sources this product worldwide, stores it at its 100-acre facility, and supplies it to construction contractors for major projects.
With the increased focus on the environmental impact of construction projects, the company decided to commission research by Giraffe Innovation, which has worked with major corporations including Dell, Virgin Atlantic Airways, GSK; and Willmott Dixon. The life cycle analysis aimed to identify how ‘green’ Cleveland Steel’s surplus steel was, compared to newly-milled steel, which is known as prime steel. The results took everyone by surprise.
Up to 96 per cent carbon savings
The experts from Giraffe Innovation found that the greenhouse gas emissions savings were as high as 96 per cent when using surplus steel, compared to buying brand new steel. Refurbishing existing tube was also far more environmentally friendly than sending it back to the steel mill for recycling. The life cycle analysis considered a comprehensive range of factors, including material processing, logistics, and disposal of any generated waste.
The reuse of steel and extended product life provided by Cleveland Steel means that its 45-year business model is clearly aligned with the key principles of the circular economy. Repurposing pipe provides a substantial reduction in the carbon footprint of a core building material – which can help construction contractors meet their sustainability obligations. It can be incorporated within a BREEAM assessment, the world’s leading sustainability assessment method for major construction and infrastructure projects.
Sustainability
Sustainability is not simply a buzzword for Cleveland Steel: it is embedded in the company’s culture. Other initiatives include incorporating electric cars into its corporate fleet – a highly unusual step for a business based in rural North Yorkshire – and investing in the preservation of woodland. The company is a member of the Association of Sustainable Building Products, UK Green Building Council and Supply Chain Sustainability School, helping it to contribute to a growing culture of sustainability at the British Constructional Steelworks Association.
Cleveland Steel recently completed a pioneering construction project for its sister company within the Bianco Group, National Tube Stockholders. The company utilised steel from a cancelled construction project for the frame of the warehouse and – applying typical Yorkshire practicality – even the soil displaced during the levelling works was taken away and reused by a local farmer. Crucially, the project delivered the warehouse at a fraction of the average cost, delivering savings of £40 to £65 (€46.40 to €75.41) per square metre compared to a conventional new build portal frame structure with a large span and high eaves. Repurposing the steel also substantially reduced the carbon footprint of the construction phase.
Customer base
Cleveland Steel’s core customer base is comprised of major civil engineering and construction contractors, who purchase steel pipes for infrastructure and national construction projects.
High-profile structures that contain steel supplied by Cleveland Steel include the Olympic stadium in London; the roof of Wimbledon Court, and the London Eye. Cleveland Steel’s strong export customer base has purchased pipes for projects as far afield as Australia and Hong Kong.
The company holds 70,000 tonnes of pipe on 100 acres at its headquarters in North Yorkshire, UK. This enables Cleveland Steel to provide very short lead times to its client base, along with highly-competitive pricing.
Independent testing by UKAS-accredited testing labs analyses the material’s properties, demonstrating compliance with customers’ specification requirements. The majority of its pipe is sourced as steel mill, oil and gas surplus production. If required, Cleveland Steel removes any coatings on the pipe and disposes of it responsibly – and can shot-blast the steel if required. It has in-house capabilities for inspection, cutting, welding, shot-blasting and coating.
Case study: the London Olympic stadium
The Olympic Development Agency (ODA) was charged with delivering the most environmentally friendly games ever, which included examining all aspects of the construction of the stadia and infrastructure for its carbon impact and sustainability. Watson Steel is part of Severfield plc, the UK’s market leading structural steel company. Watson Steel was contracted to construct the roof of the Olympic stadium in London, which required 3,850 tonnes of steel.
The contractor was concerned at the long lead times for the prime steel required for this project, so it proposed the use of surplus steel to the ODA. The ODA approved the use, based on the much lower carbon footprint of surplus steel. Cleveland Steel also commissioned extensive testing to demonstrate to Watson Steel that the 12 metre lengths of steel tube exceeded the required grade.
In total, Cleveland Steel and Tubes (CST) supplied 2,500 tonnes of surplus steel for the stadium roof trusses, representing 65 per cent of the steel used in the roof and 20 per cent of the total steel used in the entire stadium.
CST’s early involvement in the design stages of this flagship project enabled the stadium to be completed ahead of schedule and below budget, while also helping to significantly reduce the structure’s carbon footprint.
The 80,000 seat Olympic stadium in Queen Elizabeth Olympic Park, London, formed the centrepiece of the 2012 Summer Olympics and Paralympics. It was the venue for the track and field events as well as both the opening and closing ceremonies. In 2013 it was repurposed as a 60,000 football and athletics stadium; and reopened in 2016 as the home of English Premier League club West Ham United. This is another fine example of reuse.
Roy Fishwick
Managing Director
Cleveland Steel & Tubes Ltd
+44 (0) 1845 577789
www.cleveland-steel.com