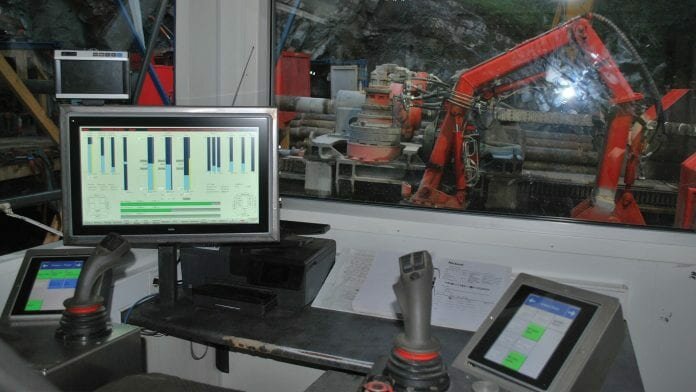
Norhard AS provides an insight into its sustainable hydropower drilling process for hydropower plants.
Established in 2007, Norway-based SME Norhard AS is full-service provider of drilling and lining services for the building of pressure shafts in hydropower plants. Since the company started, Norhard has specialised in the development of an innovative new technology for full profile, directional sustainable hydropower drilling, providing the most environmentally friendly and cost-effective solution for the Small Hydro Power Plants (SHPP) market.
Norhard’s goal is to advance the game-changing technology, by further reducing the environmental impact and investment costs of developing hydropower infrastructure, and consequently facilitate the expansion of the sector as a major source of renewable energy. The Norhard sustainable hydropower drilling concept is based on drilling pressure shafts upwards from the lower side of the mountain, with increased directional drilling capabilities and trajectory accuracy to avoid the huge environmental impact and economic costs of currently used methods – drill and blast (D&B) and rise boring (RB) – and eliminate the need for constructing roads to the mountain top.
Norhard’s sustainable hydropower drilling technology incorporates several proprietary technologies, that uses in-house and off-the-shelf components, integrated by a highly specialised technical/engineering team. After intensive research and development (R&D) activities and testing, Norhard has successfully commercialised the technology in more than 20 SHPP in Norway.
As the technology has proven its worth in the initial market of the hydropower sector, the company is now supplying efficient solutions within other business sectors as well. The Norhard sustainable hydropower drilling technology has the potential to be imperative for further development of efficient underground systems – some of its purposes and applications include:
- Supply systems for gas, water, sewage and drainage;
- Disposal systems for waste, sewage and drainage; and
- Relocation of overhead lines to underground.
The fact that more than half of the world’s population are living in cities, and that the public’s focus on sensitive landscapes is increasing, means there is high demand and a need for more sophisticated underground systems.
Traditional waterways for SHPP consist of an intake structure, a tunnel or horizontal pipe, and a penstock or pressure shaft to the power station. Many penstocks are built above ground or buried in a ditch to limit development costs. Such constructions are efficient when the landscapes are not overly challenging, however, many of the remaining potentials, especially in the most developed countries, are challenging. Topographical conditions (i.e. steeply inclined slopes with exposed rocks or risk of landslides) and new environmental regulations against the construction of aboveground penstocks, call for alternative, sustainable hydropower drilling solutions to develop underground waterways.
Traditional alternatives for technically challenging hydropower schemes include the construction of a horizontal drill and blast technique tunnel, and a pressure shaft using RB technology. The D&B technique consists on drilling a number of holes into the rock and filling them with explosive charges. After the detonation, the rock collapses, then after removing the debris, the process is repeated until the desired length of the horizontal tunnel is reached. D&B is a costly technique with huge impacts on: human toxicity, photochemical oxidant formation, particulate matter formation, acidification of soil, and large CO2 emissions ranging from 0.4 to 1.4 tonnes per meter – depending on the tunnel cross section. Normally, D&B tunnels will not be less than 20m2, even if the cross section needed for the water, flow is in the range of 0.5m2-1.5m2 for an average SHPP. Rise boring has limited directional capabilities; therefore, the majority of the time, the D&B horizontal tunnel has to be extended more than necessary in order to connect with the vertical shaft. In addition, the RB can only drill downwards from the water intake and requires transportation of heavy drilling equipment to the mountain top. This leads to the requirement of temporary access roads being built, which illuminates notable imprints over the landscape, and implies extra costs depending on the actual terrain.
The Norhard technology is a disruptive, full profile, directional sustainable hydropower drilling solution that significantly reduces the environmental impact of constructing hydropower pressure shafts, and reduces development costs, facilitating the expansion of hydropower generation. The technology does not use explosives, which represents an average reduction of 140 tonnes of CO2 emissions per hydropower project developed with Norhard technology when compared with alternative D&B and RB technique. Furthermore, by eliminating the use of explosives, the sustainable hydropower drilling technology improves health, safety and environment (HSE) impacts on workers, reduces hazardous activities, eliminates human toxicity problems, photochemical oxidant formation, particulate matter formation, and acidification of soil.
The Norhard technology incorporates an in-house developed electric drilling motor directly attached to the drill bit, and a non-rotatory drill string, which reduces to a minimum the friction between the drilling string and the rock; it consequently cuts the system’s overall energy consumption down to only 60 kW (i.e. approx. 50% lower than competing solutions). The non-rotatory drill string enables incorporation of electric cables to power the drilling motor, inclusion of high capacity fibre cables to drive the communication system – a key enabler for the automatic trajectory correction module, to compensate for direction changes due to different rock structure/quality (accuracy: 0.04 degree true north, 0.01 degree pitch), and for real time on-line positional monitoring. The integrated systems are enabling to follow pre-defined drilling trajectories and reaching the planed breakthrough point with a deviation lower than 1m per km drilled.
Trajectory accuracy and the capacity for sustainable hydropower drilling upwards over long distances and high head, eliminates the need for building temporary access roads to the mountain top, and further reduces operation costs and environmental impact. Road surface erosion and sediment yield, pollution of off-site waters, slope failures and mass movement, direct loss of habitat by the conversion of the original land cover into an artificial surface and indirect loss of habitat by the fragmentation of an ecosystem into smaller and more isolated patches. All these features together with reduced labour requirements (only two operators for the drilling process) makes the Norhard technology a very efficient and cost-effective directional drilling solution.
Based on the experience gained and results of consultations with potential clients, Norhard are now working with optimisation of its sustainable hydropower drilling technology in key features, which are fundamental to secure the place as a leading provider of drilling solutions, and to expand the business model across Europe and beyond. The EASME of EU under a Phase 2 project of the Horizon 2020 program supports these works. The ECO-Drilling project under Horizon 2020 is running over two years from the 1st of September 2017.
The overall vision of the ECO-Drilling project is to optimise, and commercialise the highly energy efficient, cost-effective and environmentally friendly full profile directional sustainable hydropower drilling technology. ECO-Drilling is capable of drilling upwards over long distances and high head (up to three kilometres drilling length and one kilometre altitude difference). The disruptive technology has the potential to reduce the cost of constructing a hydropower plant’s pressure shaft by 50%. In addition, the technology supports the development of hydropower plants at locations currently unfeasible because of technical or environmental challenges, and thus contribute to increase the share of renewable energies.
The main focus of the ECO-Drilling project over the first period has been to do comprehensive work on design and engineering to optimise the sustainable hydropower drilling technology. Experiences gained from operation of the existing equipment under various conditions and various market requirements, mixed with excessive studies on design of the overall system, as well as for specific solutions, has given great results that are in line with the objectives as planned for.
A new surface rig design is ready for piloting. The new surface rig has a completely new design and is capable to transfer a substantial amount of power to the drill string connecting the surface rig to the unmanned equipment travelling in rock. The flexibility and mobility is a challenge. In order to compromise between mobility and need of assembling and disassembling from one project to another, the surface rig is designed in two versions. One light version surface rig designed for helicopter transportation, in addition to the main surface rig design that is prepared for transportation on its own belts, or for transportation on wheels, assisted with a wheel loader or similar. The design is flexible for use with drill rods 3 m or 6 m connected with flanges or by screwing. The surface rig is able to serve several different borehole assemblies with different characteristics depending on diameters, slopes, geological conditions, lengths etc. The optimised design developed under the ECO-Drilling project enables drilling diameter in range of 0.4 m to 1.5 m over lengths up to 3 km and over differences of elevation up to 1 km. The previous experiences for the Norhard sustainable hydropower drilling technology has been length up to 1.5 km and over differences of elevation up to 500 m.
Water supply from outside and into the active drilling equipment is over hoses connected to the drill string. Coiled hoses with specifications on diameters and pressure adapted to the features of each project are separate modules of the surface rig. Coiled solutions allow continuous circulation of water when inserting new drill rods in the drill string; it is an important design criterion for Norhard’s sustainable hydropower drilling technology to utilise clean water without any additives for transportation of cuttings out of the tunnel, independent on whether drilling on an upward slope or over horizontal stretches.
The modules of the surface rig are equipped with a small computer unit for control of the local distribution of commands and collection of operational data. Each of these units – communicating over a data net – connects all the modules of the surface rig to the main computer, located in the control cabin. The distributed structure is efficient and makes it easy to handle use of varying modules in a surface rig set up between projects with different features.
Huge efforts have been expended in making available screens which demonstrate the control system and the control loops built into the software to improve the understanding and to enable the operator to efficient follow up of the operation. The operator is controlling the complete system via a single screen in the control cabin; the man machine interface now in place is efficient. Standard communication symbols, standard screens for different operation modes, good overview of alarms, and critical levels are important for the technical performance and for the overall quality of the HSE conditions during the operation of the sustainable hydropower drilling technology.
Systems are in place for continuous collection of all data for the processes. Additional programs aggregate huge amounts of data into useful information on understanding of performance and understanding of the consequences on operative actions on the performance of the processes. All data from manual and automatic logging at the sustainable hydropower drilling site are prepared for distribution over internet for further processing.
The integrated systems for navigation and steering is an important part of the ECO Drilling System. Accuracy compared to predefined drilling path and position of breakthrough is an important selling point. Smooth curves without sudden changes are important for instalment of steel lining after drilling.
The steering is very sensitive for small changes in geological conditions and for minor changes in tolerances caused by wear and tear of drill bits and the mechanical parts guiding the drill head. Constant follow up is necessary to avoid unregularly.
A software system is in place for testing during the piloting period of the sustainable hydropower drilling process. All the dynamic calculations are integrated. A presentation system gives information to the operator or other personal connecting over the net on the relation between the actual position and the settings of the steering. The software system generate advice on further operation of the steering in order to reach the planned break through point with minimum changes of the drill path.
The close follow up and analysis of the steering function has a secondary functionality. Helpful information on assessment of wear and tear and eventual mechanical faults in the drill head is available when following up on sudden changes or irregularities in the steering input and the response of it.
The aim is to have full integration of the navigation system, the steering and control system, and to include an advanced self-learning functionality with automatic and dynamic setting of the steering joint. High grade of dynamics related to geological conditions even within short distances of a specific project, as well as between different projects and changes related to wear and tear of the sustainable hydropower drilling equipment, makes this an ambitious aim that requires tight follow up and understanding of the actual geological conditions.
Large scale piloting of optimised functionality is a major technical activity over the last period of the ECO-Drilling project through the winter 2018/2019.
Askjell Tonstad
CEO
Norhard
+47 91 18 64 37
www.norhard.no